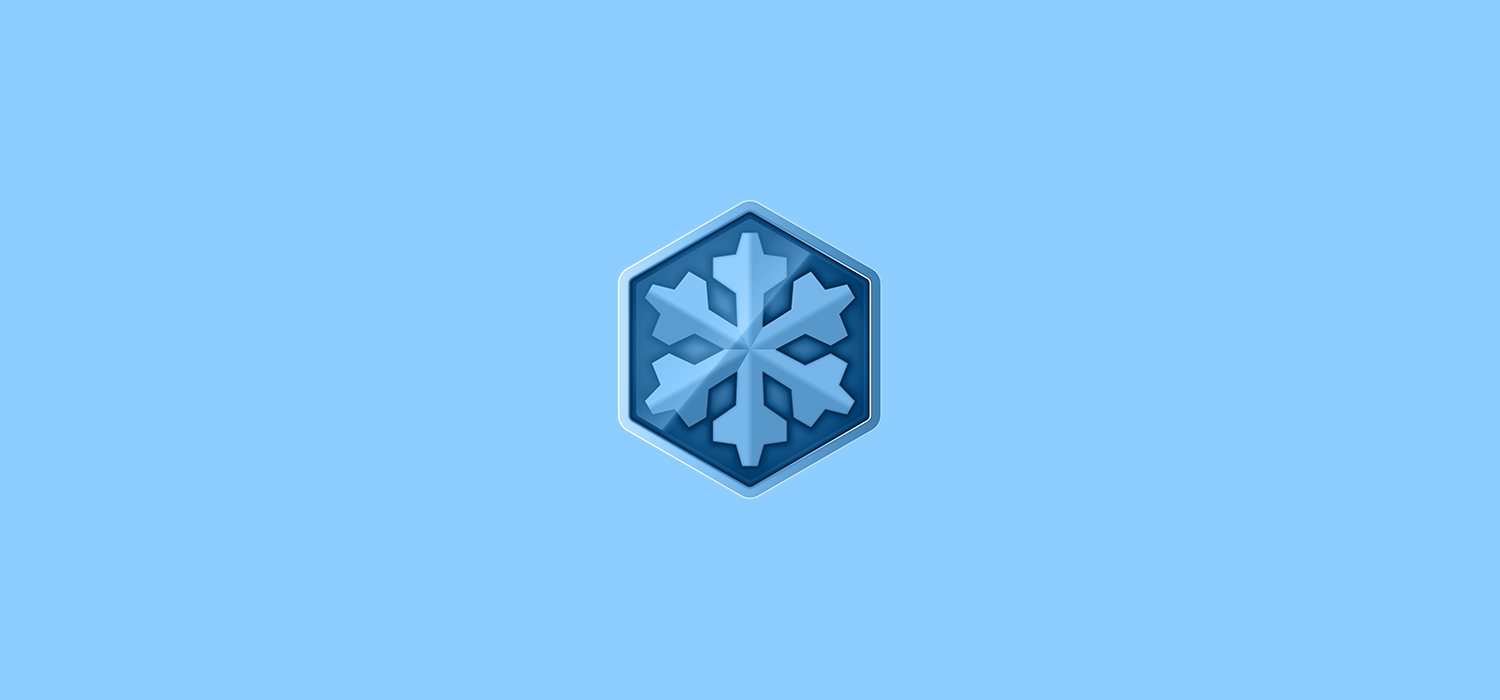
Kvikühl - Design Engineering

The Kvikühl backpack was designed as part of the capstone project class that all mechanical engineering students at the University of Pennsylvania take in their senior year. The backpack uses a steel chassis to create a space between the user's back and the backpack contents. A custom tangential fan and air channel were integrated with the exhausting straps for the complete forced convection system that served to remove sweat from the users' back. I was responsible for mechanical design, manufacturing, and branding for the project.
Purpose | Academic: MEAM 445 + 446 - Senior Design
Tools | SolidWorks, Sheet metal lasercutter, Ceramic line heater, Sewing machine, Adobe Creative Suite
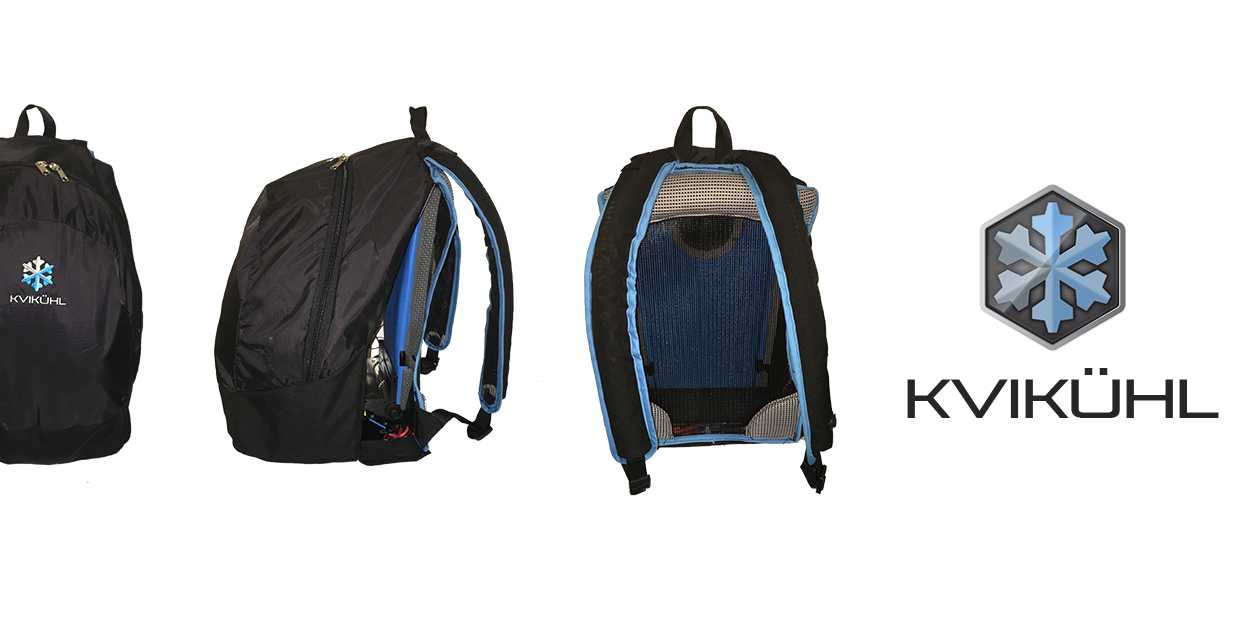
Background
Problem: Travelling to and from class in the Spring, Summer, and Fall months in Philadelphia can be very uncomfortable at normal conditions. Add a heavy backpack and by the time you get to class, your shirt is uncomfortably wet and you need a shower. As a team of four mechanical engineers, we were tasked with creating a novel, mechanical system for our senior capstone project and we chose to tackle the issue of sweaty back as a result of carrying a backpack in the warmer months of the school year. Our final solution was a backpack that keeps you cool by separating the bag contents from your back and providing active cooling through a forced convection system along the back and through the straps.
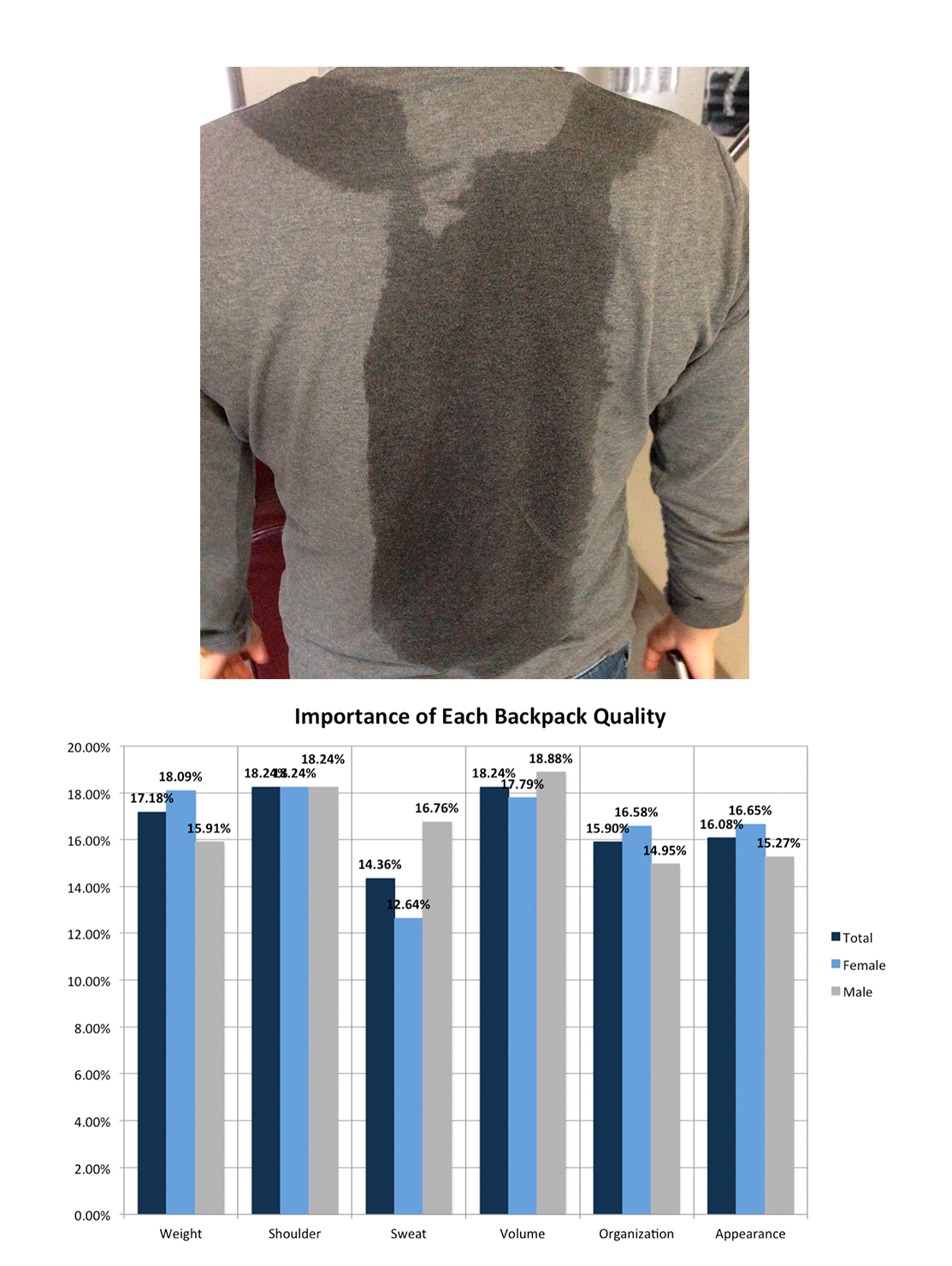
Research
We first tried to understand if this was truly a problem. Noting the performance of current backpacks and the results of a survey of 84 students, we determined that current solutions did not sufficiently address this issue.
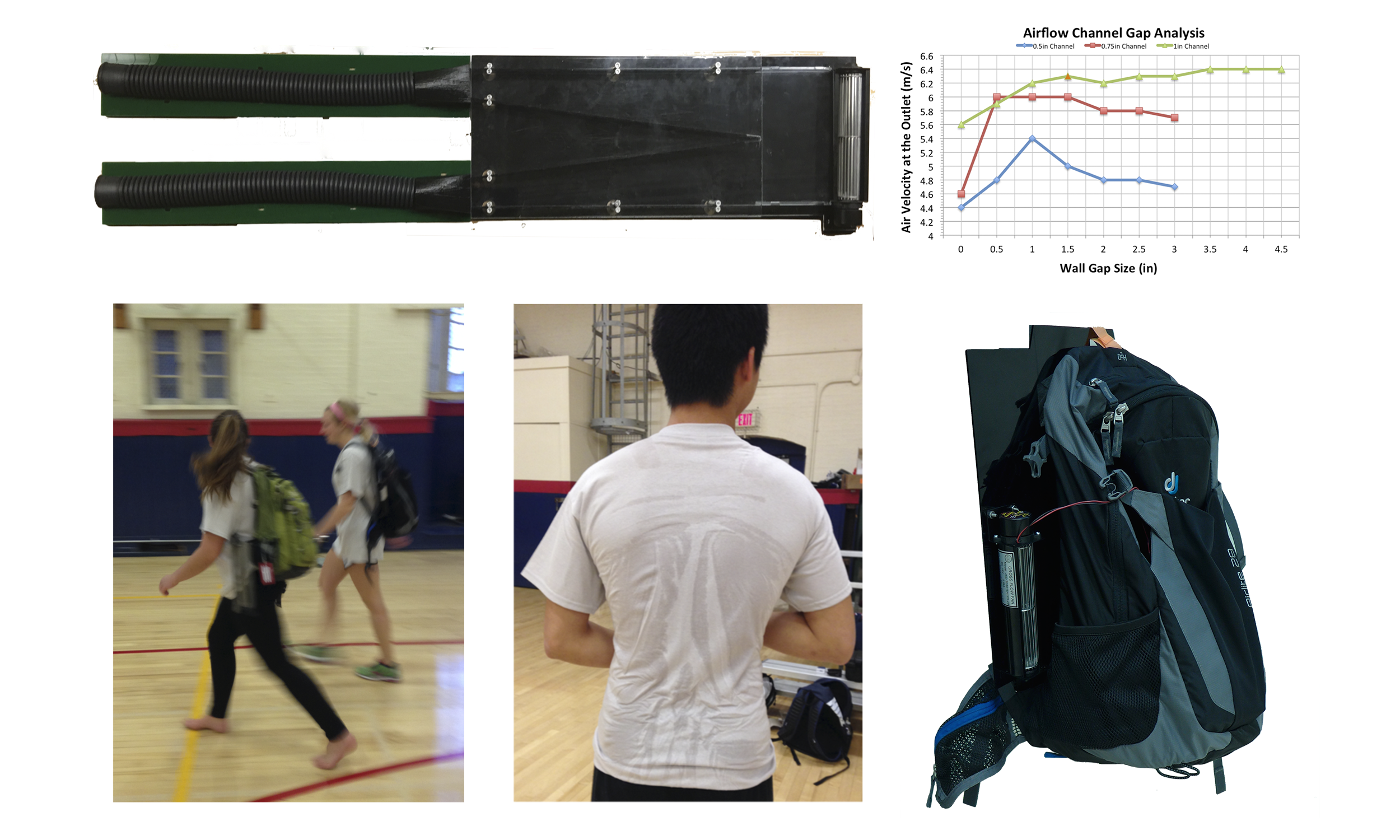
Intermediate Prototyping
After exploring different options for personal cooling tech, we determined forced convection combined with a load redistributing chassis was most inline with the body’s natural cooling method: sweat. We made quick benchtop setups in order to test system level solutions and a proof of concept prototype with an existing hiking backpack to show the efficacy of forced convection.
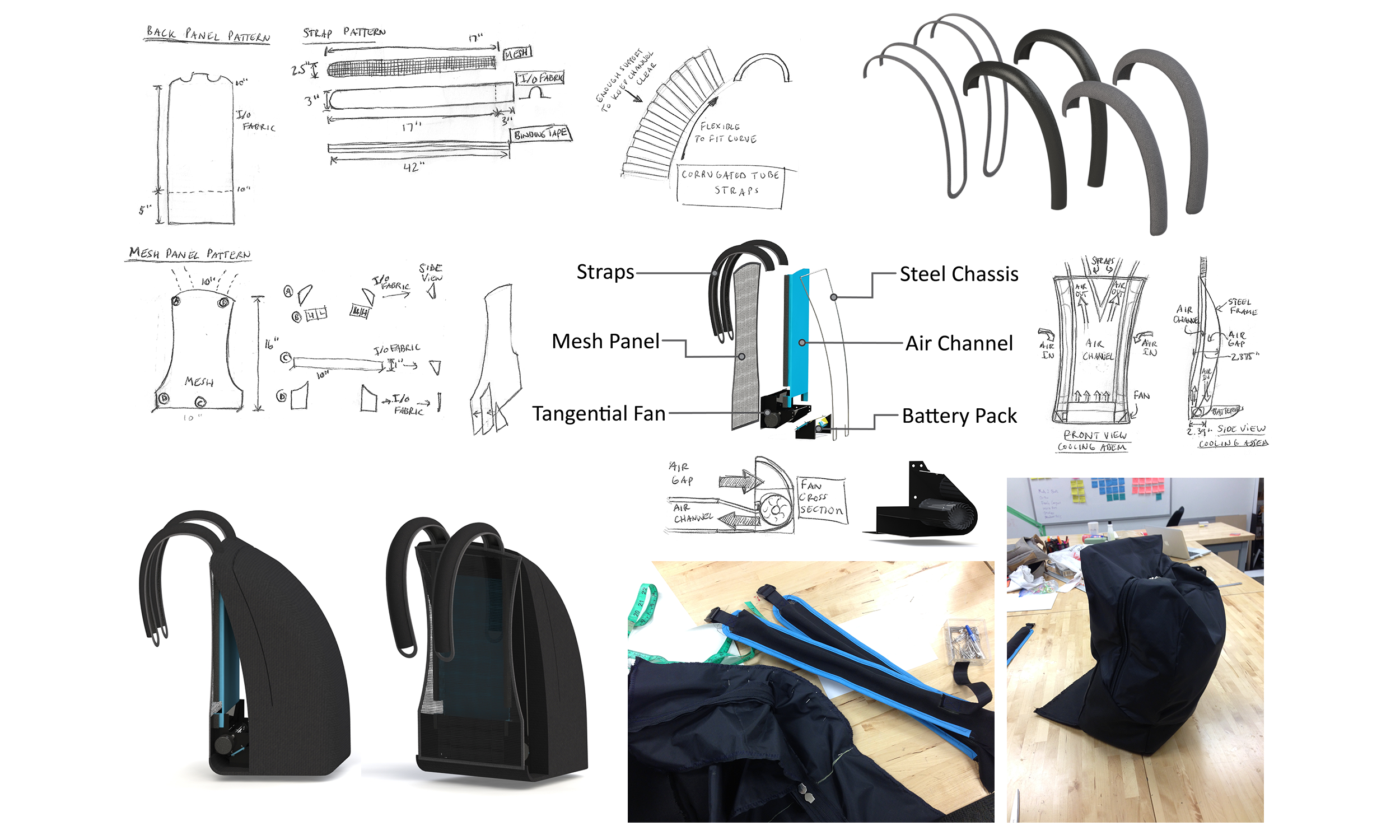
Final Prototyping
Having determined we were on the right track with our design decisions, we created the fully integrated final prototype. In order to meet our weight and packaging goals, we could not use an existing backpack. I was responsible for designing and manufacturing the air channel, straps, fan housing, steel frame, and backpack itself.

Validation
We had 22 testers walk for 15 minutes in a hallway with simulated Philly weather conditions with a standard backpack, hiking backpack, and Kvikühl backpack to determine the efficacy of our final prototype.
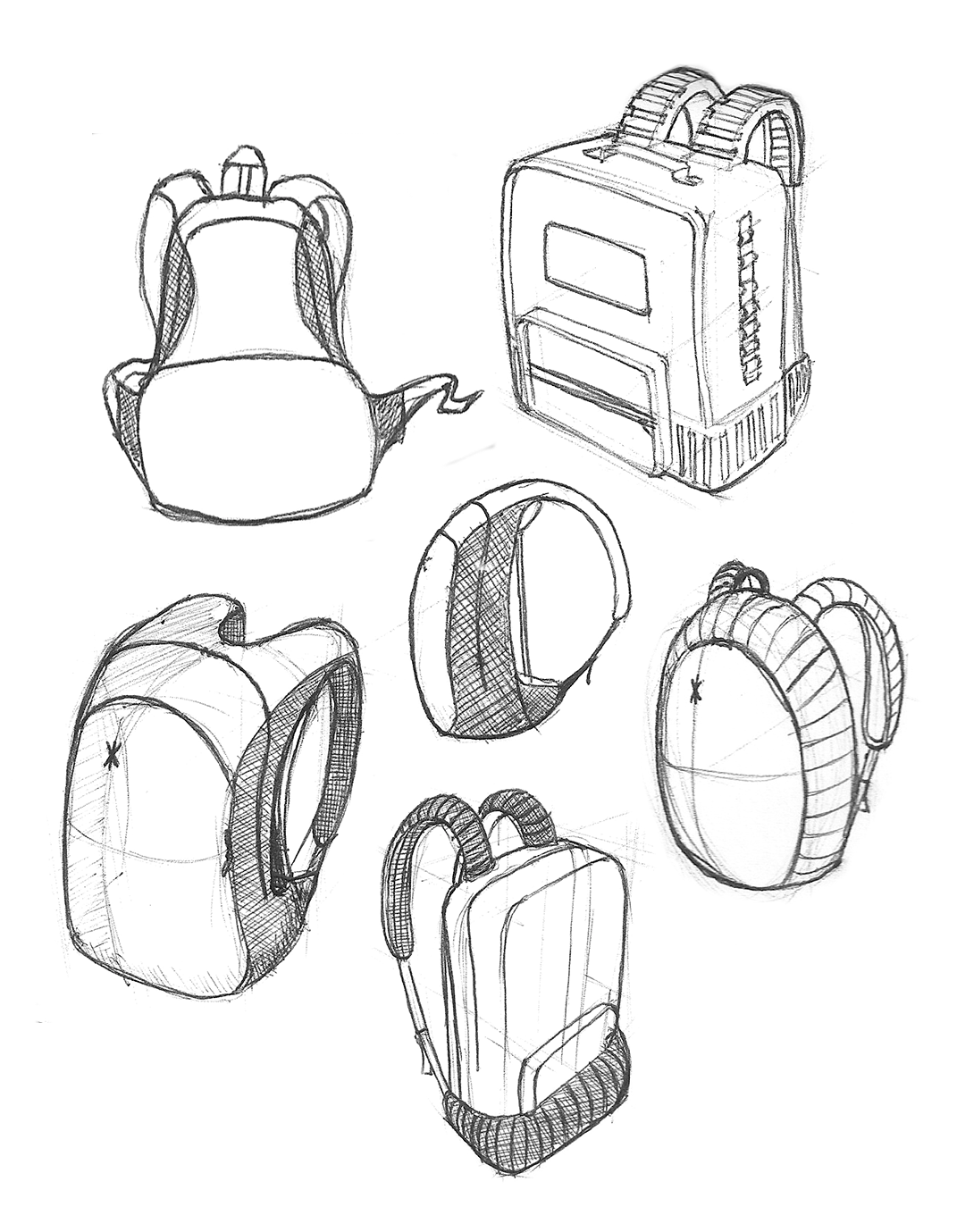
Further Development
The project ended at the prototype validation stage; however, I wanted to explore the potential aesthetic since it was a mechanical engineering project and this was never the focus.